Predictive Maintenance IoT Reduce Costs with IntelliSoft Circuit Diagram Essentials of the Predictive Maintenance Function. The operation of maintenance systems is based on such latest IT trends as fog computing, big data, AI and ML, deep learning, and cloud computing. IT specialists design IoT platforms adjusted to the needs of the specific projects. They equip systems with necessary devices and ensure stable data
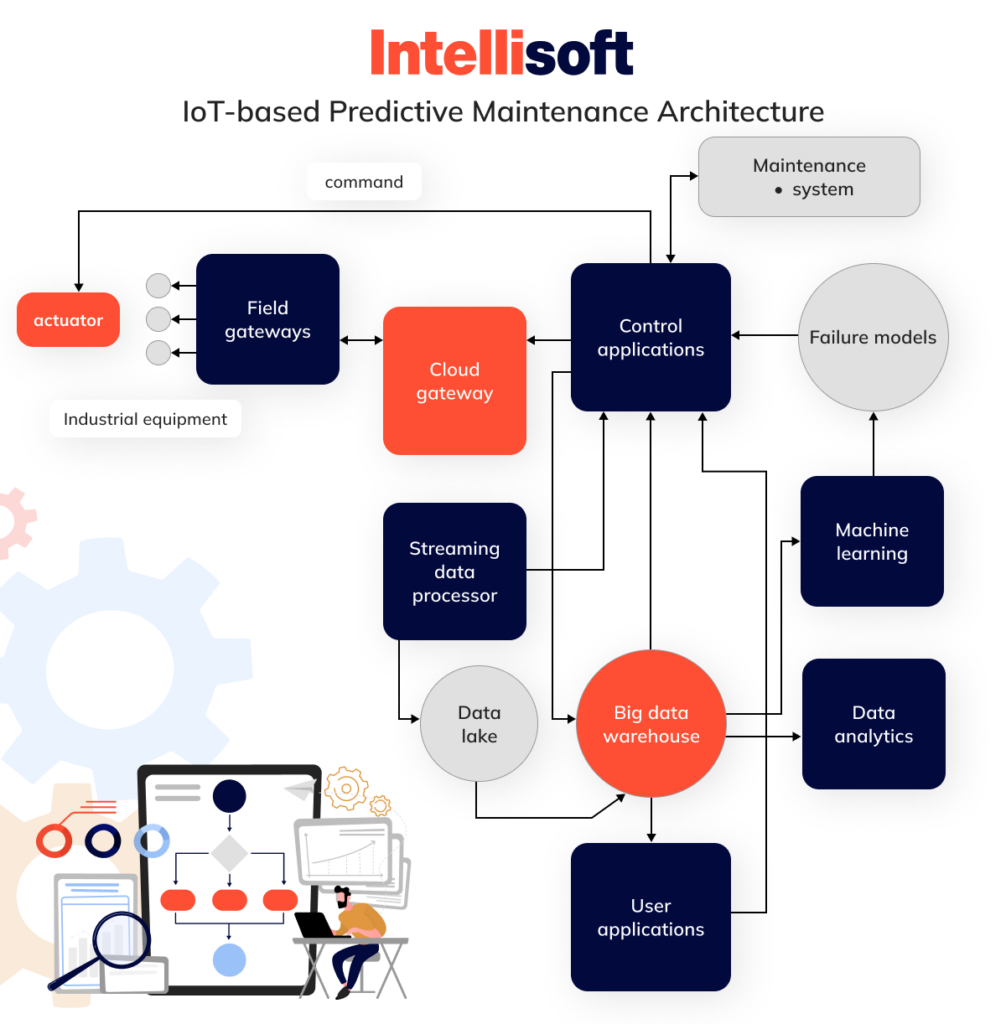
What is IoT Predictive Maintenance? IoT predictive maintenance is a method of predicting when equipment or machinery will likely fail using data collected by IoT sensors. Businesses use real-time data to monitor equipment performance and make informed decisions rather than relying on a fixed maintenance schedule or waiting for a breakdown to happen.
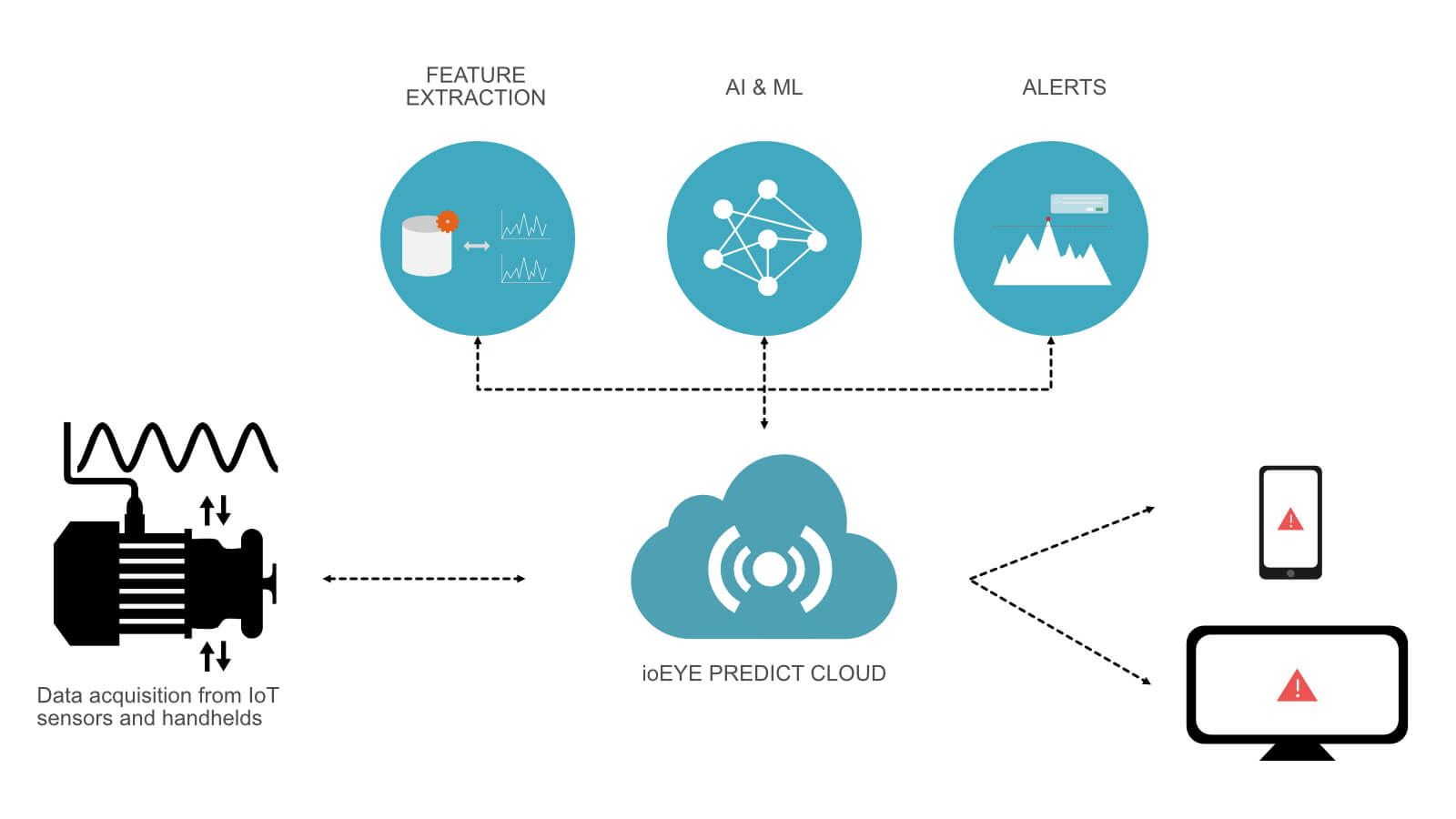
Design of Remote Monitoring and Maintenance System for Electrical and ... Circuit Diagram
Similarly, General Electric (GE) applies IoT-based predictive maintenance to monitor jet engines, preventing costly failures mid-flight. ๐น Step 2: Deploy IoT Sensors for Data Collection IoT-enabled predictive maintenance relies on smart sensors to continuously collect machine health data. Moreover, an analysis of predictive maintenance techniques, processes and tools in manufacturing systems and an integrated predictive maintenance framework is proposed in [20]. That framework is composed of three components, namely data collection and analysis, information management and a dashboard for sustainability maintenance.

Six benefits of IoT-based predictive maintenance. IoT predictive maintenance deploys the IoT technology to study a production system in real-time and forecast when and how a malfunction may occur in its component(s). In the following section, we will look at all the six benefits IoT predictive maintenance offers:
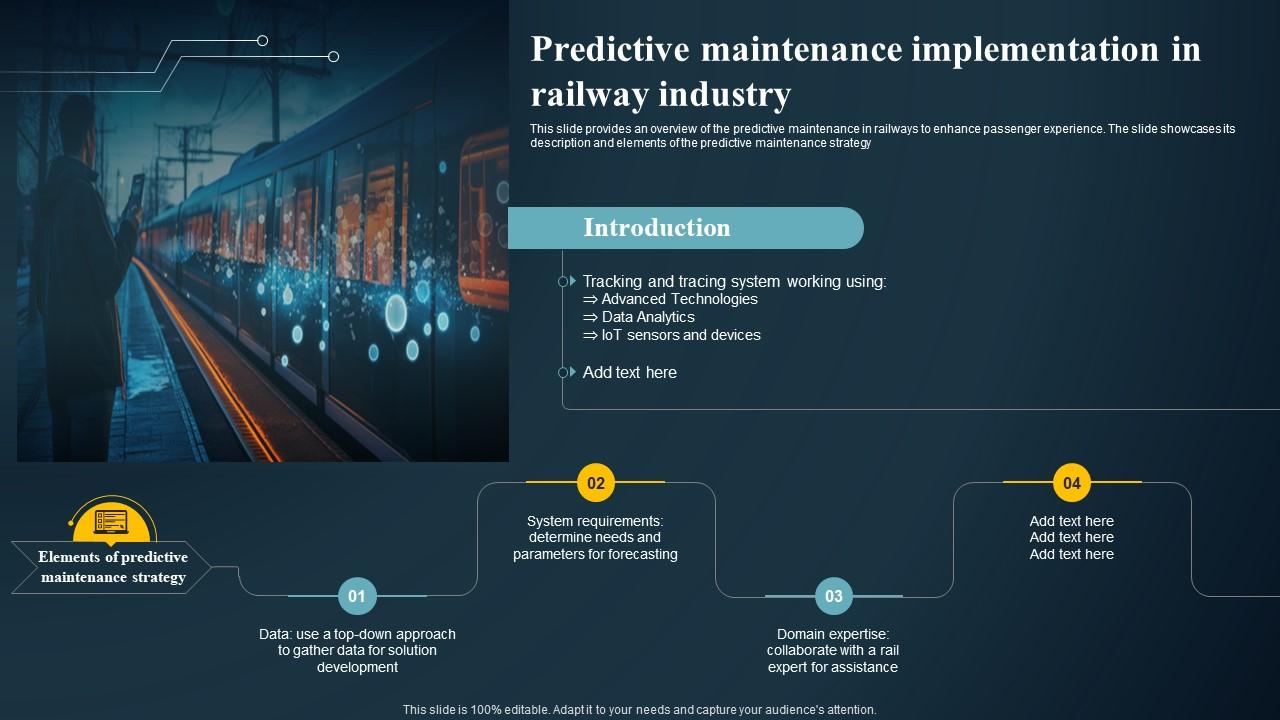
Based Predictive Maintenance System for Industrial Machinery Circuit Diagram
IoT predictive maintenance involves using the Internet of Things to collect and analyze data about equipment and machinery. Sensors and monitors gather real-time data on equipment status and performance. This data is then processed by predictive maintenance software or other smart systems to identify potential issues that could lead to downtime. [1] IoT-Based Predictive Maintenance for Industrial Equipment (2018) Smith, J., & Patel, R. proposed a predictive maintenance framework for industrial equipment using IoT and machine learning. The system involves real-time data collection from multiple sensors, data processing at the edge, and cloud-based analytics to predict potential failures. The urgent necessity to design an improved predictive maintenance system that improves prediction accuracy and provides a high degree of adaptability and transparency in maintenance decision-making drives our effort [6,7,8]. In order to solve these issues, we have developed an Advanced Predictive Maintenance System (APdM) that incorporates
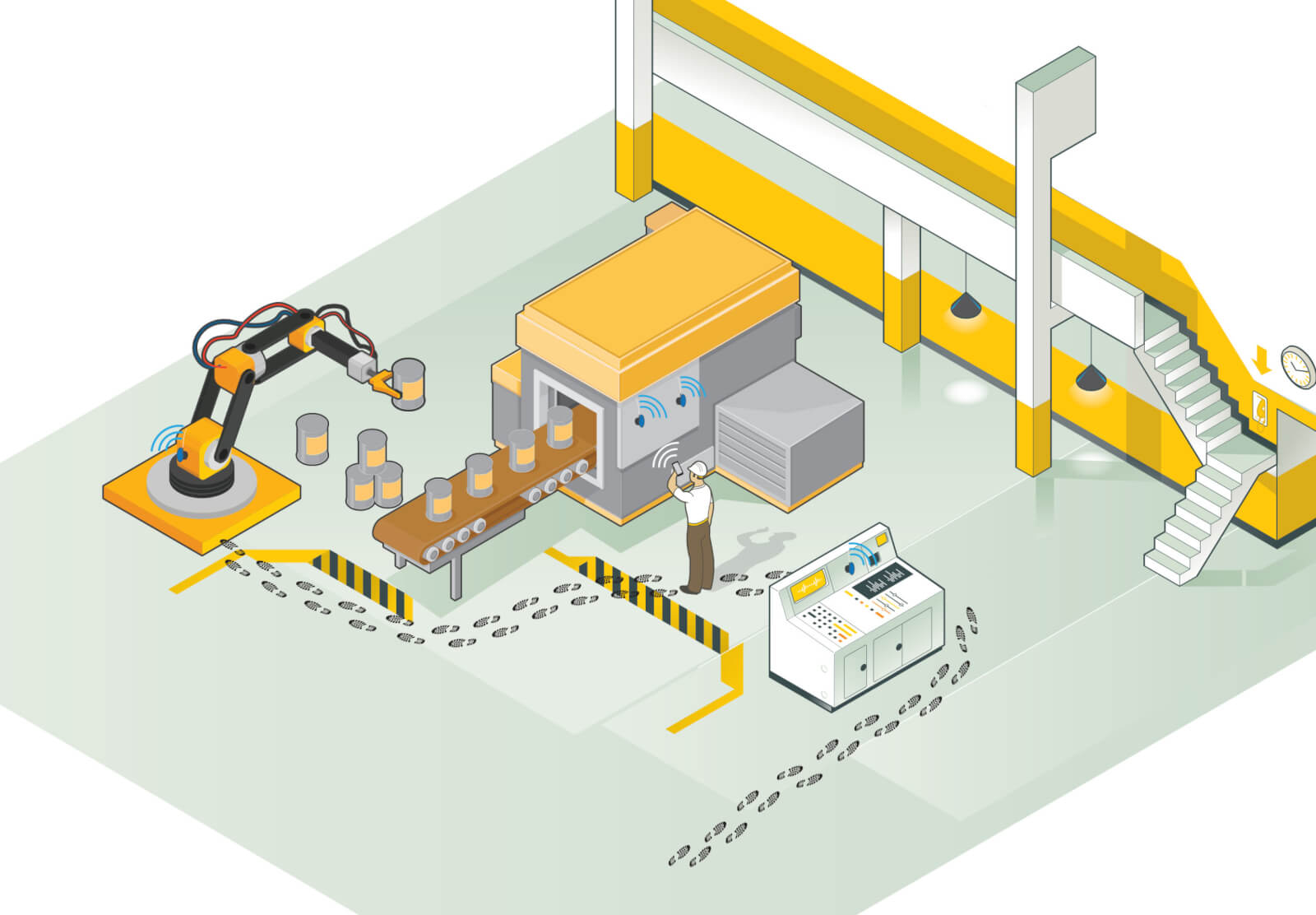